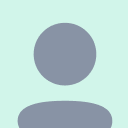
Ravi Kumar

Ketki Singh
Kaizen is a Japanese word meaning "improvement." Regarding the business understanding, kaizen refers to the activities that continually help in improving business functions and involving all employees of an organization.
In simple terms, kaizen (Kai = Change, Zen = Good/Better) means a continuous improvement by the elimination of waste. Masaaki Imai developed the kaizen concept with the primary focus on making never-ending efforts to help improve everyone in the organization.
Why is kaizen needed?
It is required primarily to carry out maintenance and innovation more efficiently.
- Maintenance includes activities which involve looking out for current managerial, technical, and operational standards.
- Innovation works on drastic everchanging improvements in the current organizational processes. Kaizen follows the road in between, which means looking out for small continuous improvements in the current organizational processes.
Who can practice the kaizen concept?
Everyone, which includes Top Management, Managers, and Workers. A framework can be seen in the diagram depicting who is involved and where is he or she involved by following the kaizen methodology at the workplace:
Kaizen works on the elimination of waste. This waste can be categorized into the following sections:
- Unevenness
- Overburden
- Non-value adding work
By simplifying kaizen processes, one can increase its utility. Kaizen involves 5S steps, which are as follows:
- Sorting – Keeping only the essential items.
- Simplifying – Eliminating the extras.
- Sweeping – Keeping the workplace clean.
- Standardizing – Standardizing the work practices.
- Sustaining – Monitoring and reviewing standards constantly.
What are the advantages of kaizen?
The advantages of kaizen are numerous. Some of them are that it reduces waste, ensures space utilization, improves product quality, and results in high employee morale and low attrition rate. Over and above the apparent advantage of improving business processes, kaizen encourages teamwork and ownership. Teams become accountable for their work, and they can make improvements to their own working experience.
The overarching purpose of kaizen is “to create a vibrant workplace where each employee makes his or her contribution.”
What is the kaizen process?
If we see the kaizen process, it includes a few major phases such as:
- Identify a problem
- Analyze the process
- Develop an ideal solution
- Implement the solution
- Analyze the result
- Publish and standardize the result
Like we know that necessity is the mother of invention; similarly, whenever a problem arises, it gives more opportunity for improvement. And once the issues are identified, the company needs to call upon the cross-functional personnel to figure out the root cause of it. The proposed solution is then tested on a small scale. The team makes modifications to the solution by using the collected data. Eventually, the results are spread across the organization, and the solution is standardized.