Figure 1: The journey of an idea
Creating a product starts with solving a problem. An idea, inspired by a need or challenge, becomes a prototype that epitomizes innovation and creativity. This first prototype undergoes a feasibility test and is demonstrated as a proof of concept (POC). An idea becomes a prototype, then a market-ready product. However, even the best products eventually reach their end, whether through wear and tear, outdated materials, or new tech, ideally with minimal environmental impact.
This article looks at key optimizations in the development of electronic products using real-world examples. It targets mass-produced tangible electronic products. It aims to educate young engineers and help business professionals, such as CTOs, understand the importance of a qualified engineering team in transforming concepts into successful products.
Navigating the hurdles in product development
Transitioning a prototype to a real-world product involves many optimization challenges. The engineering team must recognize and prioritize these challenges to effectively manage resources and meet product specifications. The following diagrams illustrate how priorities are arranged for two use case examples.
Figure 2: Solar powered IOT Gateway use care
Figure 3: Hearing aid use case
Mechanical optimizations
Electronic products must fulfil the mechanical specifications for circuit boards, considering factors like size, shape, and placement of component. Engineers must choose appropriate components and handle placement restrictions while maintaining signal integrity with effective multi-layer PCB stacks and routing techniques. It requires expertise in both electronics CAD and mechanical CAD integration.
Design for sustainability: A core design principle
Sustainability in a product refers to its ability to endure over time. To achieve this, the product's design must address several challenges, some of which are discussed in the following table.
Title | Description | Examples |
Self-sustainability (longevity) | Ensure longevity by selecting materials that are less likely to become obsolete and by offering alternatives to ensure continuity of manufacture. |
|
Market sustainability | Maintain market share without being outperformed by competitors. | A design decision to use an external current transformer in a low-power AC energy meter design is unfavorable because, as a competitor can choose a cheaper internal shunt sensor and offer a more affordable and easier-to-install product. A circuit design using a low-cost microcontroller, and an external real-time controller (RTC) chip can be outperformed by a design that uses a microcontroller with an integrated 32.768 kHz oscillator and a firmware-based calendar. This approach reduces component count, assembly, and testing time, and saves PCB space. |
Environmental sustainability | Minimize environmental impact from production to the entire product lifecycle with eco-friendly materials and manufacturing techniques. | Reduce the amount of copper that needs to be etched away in the PCB design phase, to reduce the use of harmful chemicals in manufacturing. Specify lead-free solder and recyclable components. |
Figure 4: Fixed version 5V version
Figure 5: Adjustable version
Optimizing power utilization: A universal design priority
Electronic products are powered by utility grids, renewable energy sources, batteries, or energy harvesting methods, depending on the application. Design engineers must prioritize reducing power consumption regardless of the power source.
Title | Description | Examples |
Use low-power components | Pay attention to power efficiency when you select components. | Select low-power microcontrollers and low RDS ON MOSFET switches for power switching. |
Power islanding | Add switch on/off functionality for different sections of the PCB. | A smart energy metre that transmits data every hour can deactivate its GSM modem during idle periods. The display backlight can also be turned off, when the user is not interacting. |
Avoid power-dissipating components | If other factors, such as cost, size, and EMI constrains, replace inefficient analog power circuit sections. |
|
Architect firmware for low power | Design firmware to keep the entire circuit board or specific sections in sleep or low-power modes when idle. |
|
Cost optimization: The most demanding aspect of product development
Cost optimization takes precedence in product development, particularly in mass manufacturing. Cost optimization throughout the product life cycle, such as manufacturing, servicing, and disposal, should be considered while designing.
Title | Description | Examples |
Optimize Bill of Material (BOM) | Reduce component count and use low-cost alternatives without compromising on performance. |
|
Enhance manufacturing processes | Develop designs tailored for automated assembly, streamline assembly procedures, enhance assembly ergonomics, and avoid intricate mounting requirements to lower manufacturing expenses. | Add locating pegs and snap locks in enclosures to quickly align the circuit board and avoid or reduce the use of screws. |
Ensure proper heat management | Use appropriate heat management techniques to avoid heat sinks and cooling fans. |
|
Perform testing and quality control | Implement design tactics to streamline testing efforts |
|
Ensuring safety and security: A paramount concern
Products such as ATMs, access control systems, IoT, gateways, etc. require security measures to protect sensitive data. Implement appropriate techniques during the design stage to ensure required security levels and standards.
Examples:
- Implement access passwords in firmware.
- Use secure protocols and encrypt data during communication and storage.
- Establish tamper-proof methodologies and tamper-detection mechanisms.
- Connect a BGA microcontroller's serial port to a GSM module with bottom-side pads through the inner layers of a multi-layer PCB, making it harder for a hacker to tap into the serial port and read data.
- Products may also require critical safety measures to reduce risks to humans and property. This includes techniques to improve security.
- Implementing effective surge protection techniques for power inputs and outputs is crucial. Additionally, apply static discharge protection for inputs that involve human interaction, such as keypads and touch screens.
Examples:
- Implement redundancy by including backup components or circuit boards.
- Establish default fallback states and quick stops for all moving machinery parts.
- Incorporate fault detection hardware, such as microcontroller supervisory chips and watchdog timers.
- Fix a limit switch to cut off motor power if it drives a slider beyond a set limit in case of a motor driver failure to reduce damages.
- Implement fail-safe techniques such as using a pulled-up input to detect an emergency stop switch press. This causes any connection failure between the switch and the microcontroller to trigger an emergency stop.
Figure 6: How a microcontroller works to ensure security
Design for ergonomics: A vital consideration
Ergonomics is the science of designing products to optimize human well-being and performance. It plays a pivotal role in shaping user experience, comfort, and engagement, aligning products with the natural capabilities and limitations of the human body.
Examples:
- The placement and size of buttons and touchscreens to accommodate diverse user demographics.
- The beep of a supermarket barcode scanner indicates a correct read without needing to turn and check the display. The laser beam helps align the reader easily, and factors like weight, size, shape, and table rest for easy grabbing support ergonomics.
Promote environmental resilience: An environmentally conscious design
Products must withstand environmental hazards. Enclosures should meet appropriate ingress protection (IP) levels, and designs should support maintaining this protection.
Examples:
- Using a sealed light pipe for an indicator LED to help maintain enclosure integrity.
- Vertically mount circuit boards to accumulate less dirt and condensation.
- Using a membrane keypad that provides better shielding.
Ensure adherence to compliance: A key aspect of electronic product design
Product designs must adhere to international compliance standards, such as EMI and safety. Design engineers must consider these requirements during the design phase to minimize iterations and achieve compliance.
Examples:
- Follow best practices in PCB design to minimize EMI and EMC, when high-speed data transfer and high-speed switching in power stages such as a PWM motor controller.
- Print high voltage warnings and symbols.
- Cover high voltage tracks on the PCBs with extra silk screen pours.
Futureproofing: Design for repairability and upgradeability
Design for easy repair and upgrade to extend the product's lifespan and reduce the environmental footprint associated with premature disposal and replacement. Modular design is one of the key techniques in this process.
Examples:
- Design the communication modem (GSM, Wi-Fi, etc.) as a pluggable module to allow easy replacement of faulty parts, reducing downtime. It also simplifies upgrades during technology shifts like moving from GPRS to LTE or GSM to LoRa. Though firmware updates are needed, this approach ensures that the product remains adaptable to technological advancements.
Design sustainable disposal: A commitment to environmental responsibility
Design an electronic product with end-of-life disposal for easier and safer disposal, with a low environmental impact. Ensure product compliance with environmental regulations such as RoHS (Restriction of Hazardous Substances), WEEE (Waste Electrical and Electronic Equipment) directives, and eco-label certifications like Energy Star and EPEAT.
Examples:
- Specify non-toxic and recyclable materials (ex. Lead-free Solder) for product manufacturing.
- Modular design can improve the reuse of certain parts and dismantling before disposal to improve disposal safety.
- Use standard and interchangeable components to improve reusability.
- Make it easy to remove items like battery displays, etc.
Case study: A real-world example
An electronic controller was retrofitted into an existing power distribution unit (PDU) for a leading telecom operator in Sri Lanka. This upgrade enabled remote ON/OFF control of underutilized telecom equipment across the country's telecom infrastructure facilities. The picture below is a 3D rendering of the actual circuit board designed.
Future proofing
We designed a PCB footprint to accommodate two distinct ethernet module types from different suppliers, allowing use of the other without hardware modifications if one becomes obsolete.
Safety
Optically isolated the microcontroller and related electronics from relays and chassis connections linked to battery-positive terminals in telecom use cases. This prevents accidental contact between the USB debug cable or laptop body, which is on battery negative (the circuit ground), and the chassis during troubleshooting and installation, avoiding dangerous battery short-circuiting.
Cost/environmental impact
The decision to retrofit an electronic controller into an existing PDU saved all the original parts, resulting in significant cost savings and a substantial waste reduction.
Fail-safe design
Utilized the normally closed contacts of relays to power telecom devices. Added a power switch for quick device fallback to default so that all telecom equipment is in power-on state. Implemented a firmware watchdog timer to automatically reset the controller in a stuck situation.
Endnote
During development, an experienced engineering team assesses the product specifications and technical feasibility. If they discover adjustments that can save time, reduce costs, and enhance the product, they collaborate with the client to explain these changes and their benefits, ensuring mutual agreement.
Once development and laboratory testing are completed, the team conducts field testing to verify the specifications before approving the design for mass production. This step is crucial for identifying and rectifying unforeseen issues that could otherwise lead to costly failures.
Ultimately, product development engineering is a challenging, innovative, and rewarding journey for passionate engineers.
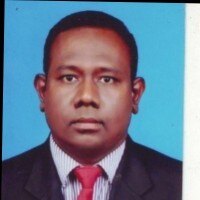